Intention :
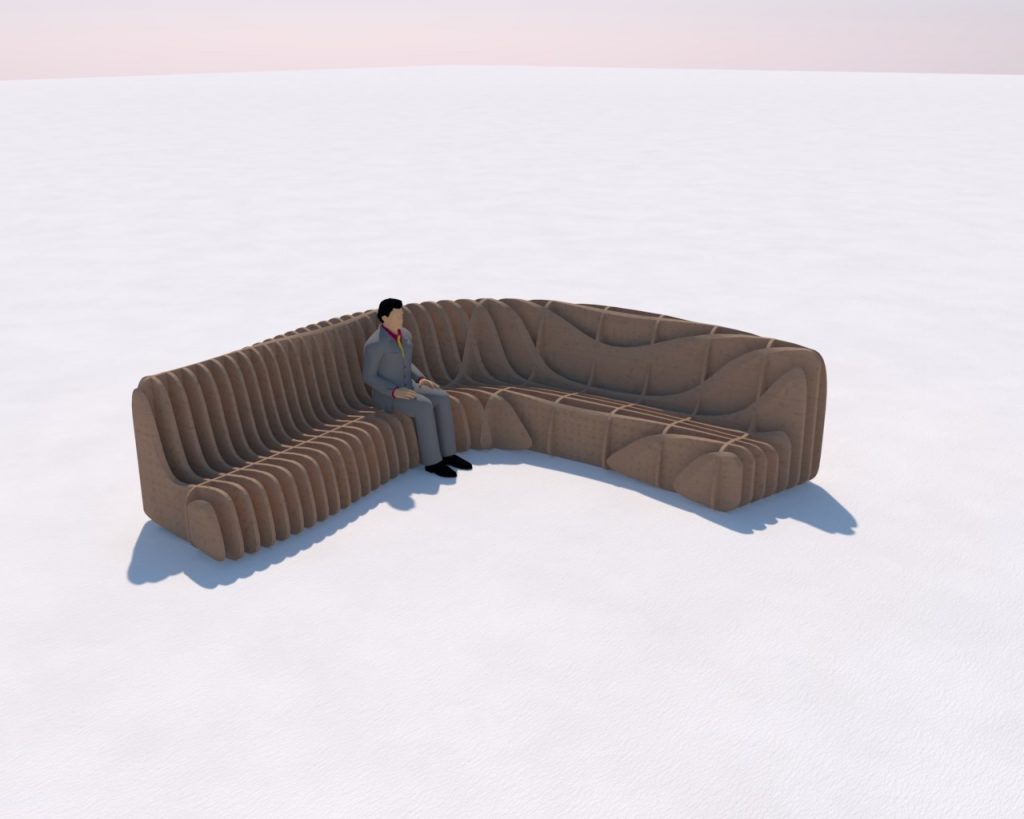
Dans le cadre du cour de CTID, j’ai souhaité réaliser un modèle 3D d’un banc dont le matériau principal serait le carton.
L’idée derrière cet objectif était de réussir à former un mobilier urbain d’intérieur en réutilisant un matériau très présent dans nos poubelles, le carton.
Le carton est un matériau régulièrement utilisé en emballage, et presque tout le temps jeter à la poubelle après ça taches accomplie
Je suis parti de ce principe pour tenter de modéliser un banc capable de réexploiter ce matériau et en partant de faces planes, réussir à former un modèle 3D
Pour la réalisation de ce mobilier j’ai choisi d’utiliser le logiciel Fusion 360. Mon objectif était de modéliser ce banc de façon a pouvoir modifier la forme a tout moment assez facilement
Réalisation :
Pour ce faire j’ai d’abord commencé à tracer la direction que mon mobilier allait avoir. J’ai choisi une vue de dessus, c’est-à-dire une vue en plan pour déterminer l’espace et la forme que mon mobilier allait prendre. La difficulté était d’obtenir une forme organique en partant d’un matériau plan. La direction a donc été précontraint afin de pouvoir venir modifier son sens à tout moment dans le processus de création.
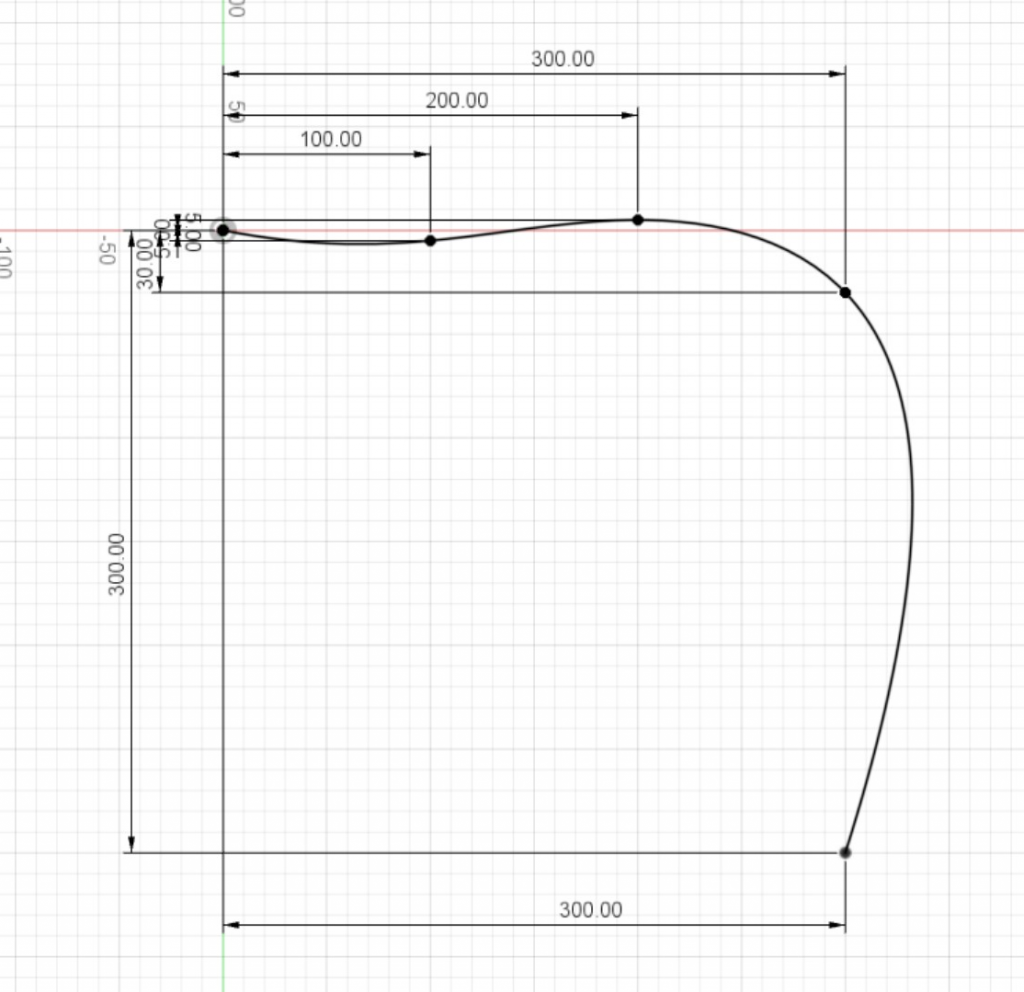
Sur cette trace je suis venu ajouter un profil. Le profil du banc. Pou se faire j’ai dû créer un nouveau plan via l’outil « plan le long de la trajectoire ». Ce plan a permis au profil du banc de se dessiner en perpendiculaire par rapport à la « trace trajectoire ».
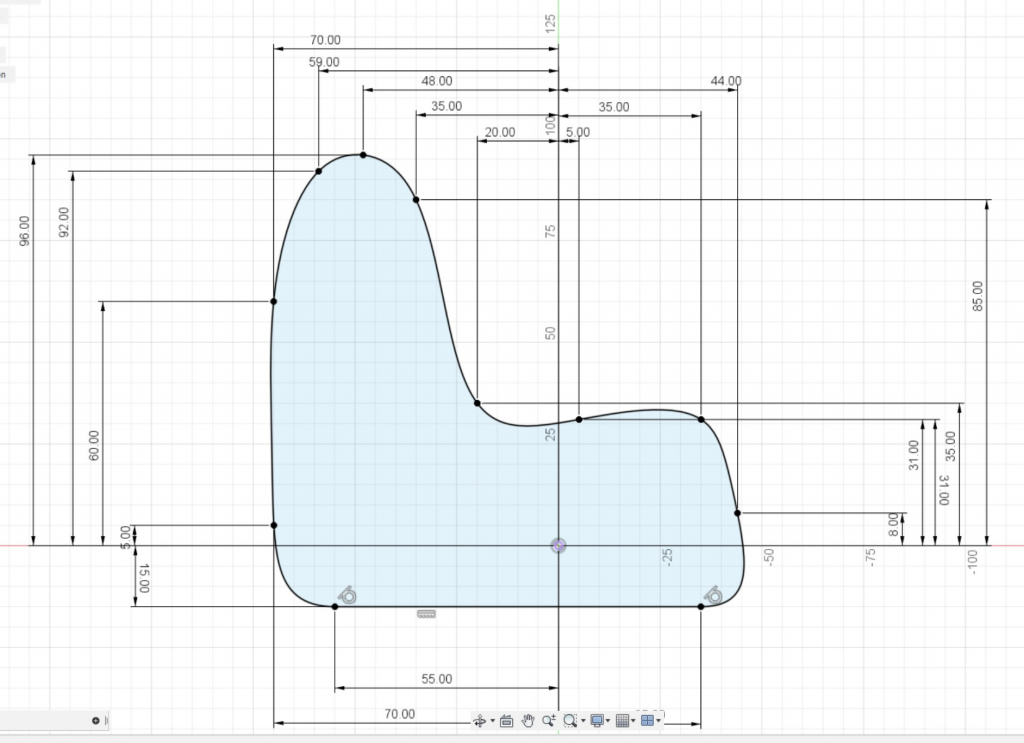
Une fois ce profil dessiner perpendiculairement à la trajectoire souhaitez du banc, il s’agissait de venir étirer ce profil le long de la trajectoire pour obtenir le volume du banc. Pour cela j’ai utilisé l’outil de balayage de fusion avec un espacement de 1 m entre chaque profil.
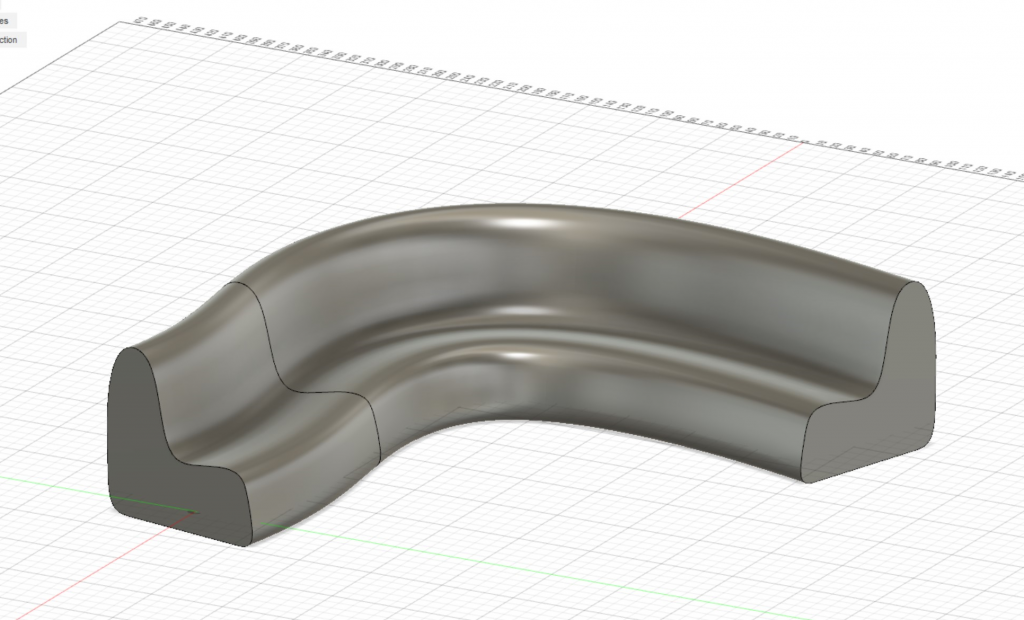
Le volume se finissait un peu trop droit. Pour résoudre e problème j’ai utiliser l’outil chanfrein pour arrondir les bout du banc et accentué le coté organique de celui-ci.
Le volume du banc obtenu il fallait maintenant faire en sorte que ce volume soit constructible à partir de carton. Pour cela j’ai voulu faire la structure du banc en nid d’abeille. Pour ce faire sur fusion j’ai réalisé un plan de décalage au-dessus du banc avec une vue en plan. Cette vue devait me permettre de dessiner la trame que mon banc allait adopter.
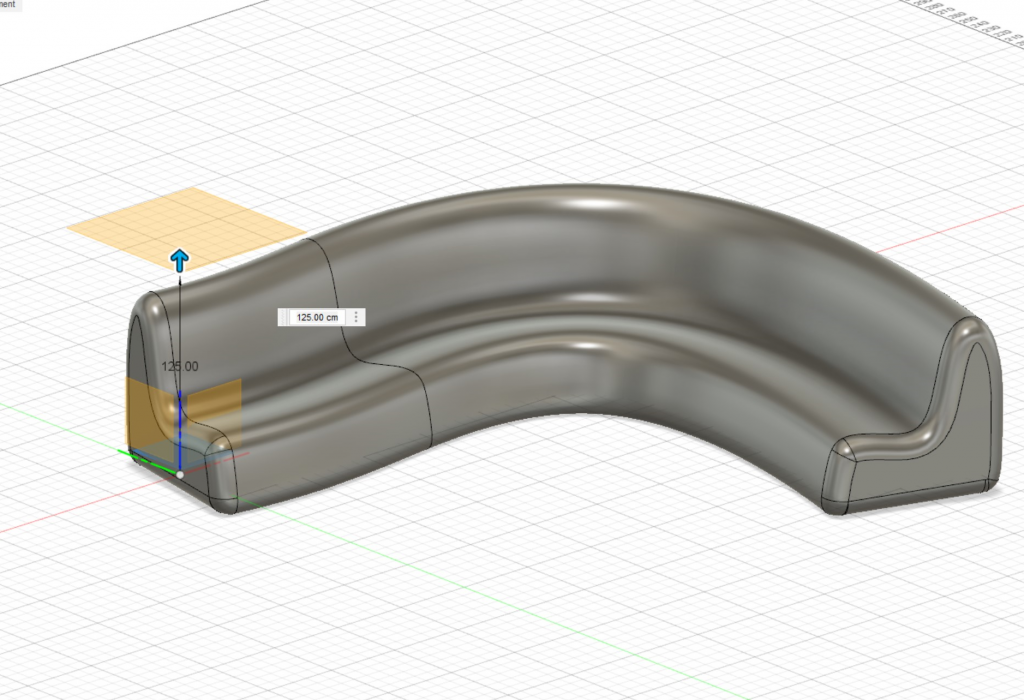
La trame à été réalisé sur ce plan. En dessinant un simple rectangle de 10 cm X 50 cm. Ce rectangle a ensuite été dupliqué sur l’axe X et Y en respectant un écart de 3 mm qui est censée représenter l’épaisseur du carton.
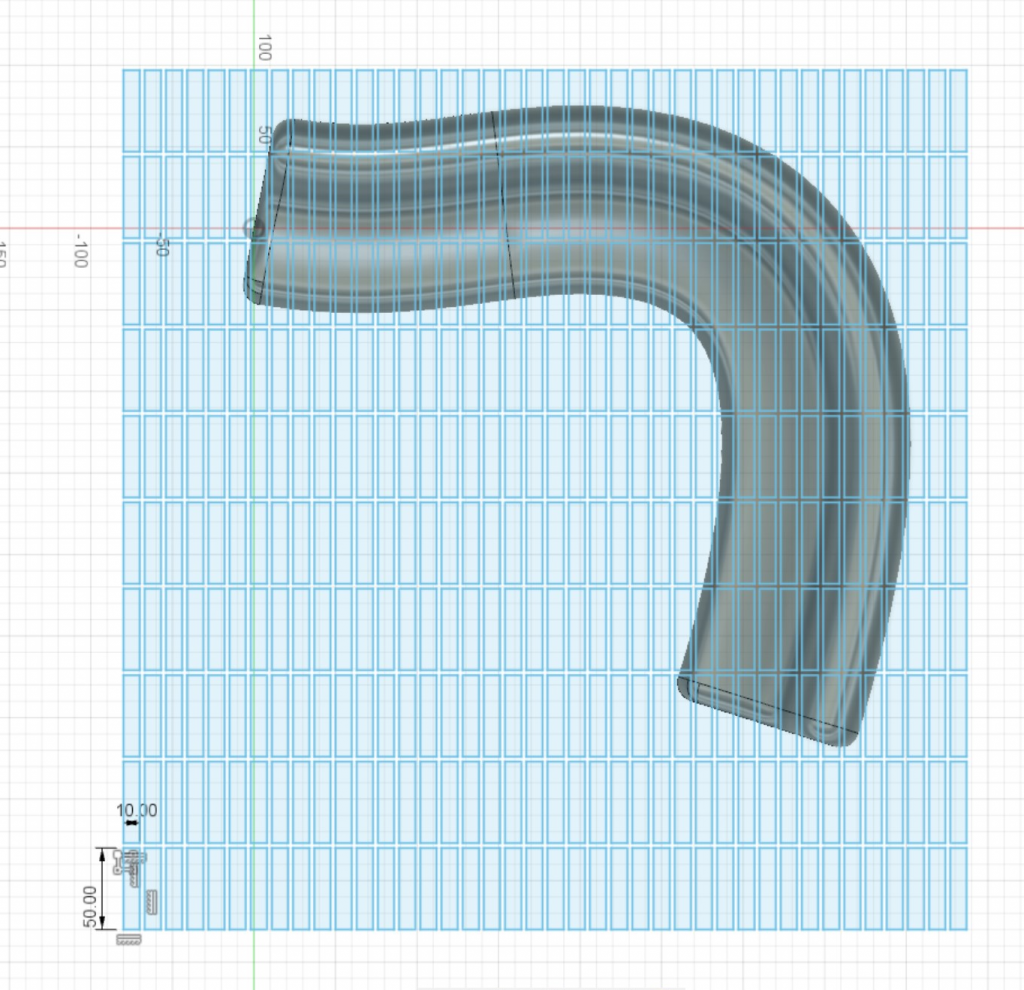
Par un simple jeu d’extrusion j’ai ensuite obtenu la forme du banc dans une version satisfaisante pour sa réalisation.
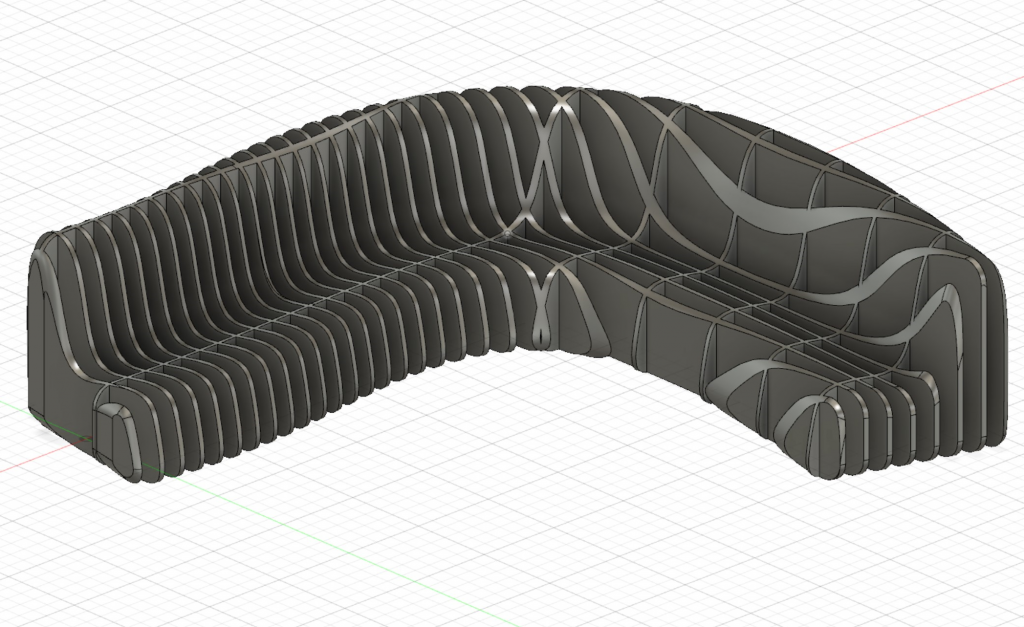
Cette méthode permet jusqu’ici de rester dans un modèle programmer et facilement changeable. Pour la suite j’ai changé de logiciel pour des raisons de rendus.
Maquette :
Pour terminer ma conception il me fallait une méthodologie pour assembler ces cartons entre eux et obtenir le volume de mon banc.
Le procéder d’assemblage par addition ( imprimante 3D ) ne semblait pas pertinent. Le carton n’étant pas un matériau pour entrer dans une imprimante 3D. L’assemblage au travers d’une découpeuse laser me semblait plus pertinent. En effet je souhaitant valoriser un circuit de récupération du carton disponible sous forme de chutes un peu partout. Pour cela une simple chute obtenue aurait pû être envoyer dans la découpe laser afin d’obtenir chaque face du banc.
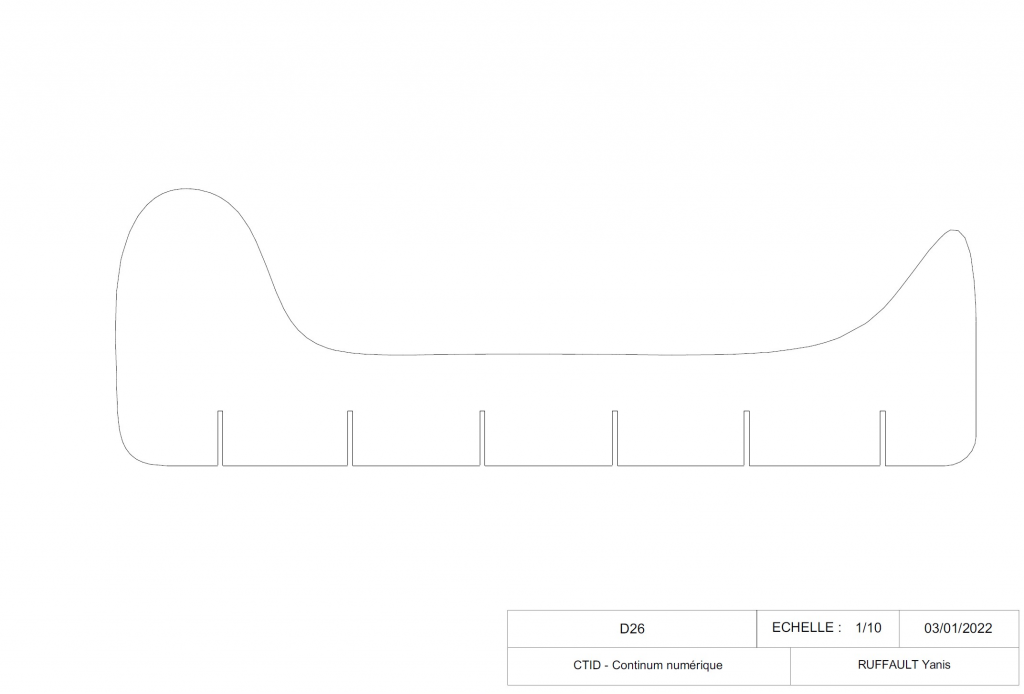
Dans un souci de repérage j’ai utilisé la symbolique C et D numéroté pour repérer chaque morceau a assembler du banc. Mon modèle compte 40 morceaux à assembler les uns par rapport aux autres.
La réalisation de ces faces est passé par un logiciel de dessin plus basique, pour que chaque face intègre aussi l’assemblage entre C et D de façon emboité.
Pour me faire une idée de mon modèle j’ai aussi tenté une impression 3D en maquette seulement. Cette maquette a été mal imprimé en raison d’un problème de bouchage de la buse de mon imprimante. Ce bouchage de buse été lié a un problème de rétractation trop élevé du PLA dans le système d’impression. Le PLA chaud remonter trop vite dans le refroidisseur ce qui avait pour effet de boucher la buse. Ce problème est aujourd’hui résolu mais je n’ai pas retenté d’impression lié au fait que j’avais obtenu un morceau suffisant pour représenter mon banc en maquette.
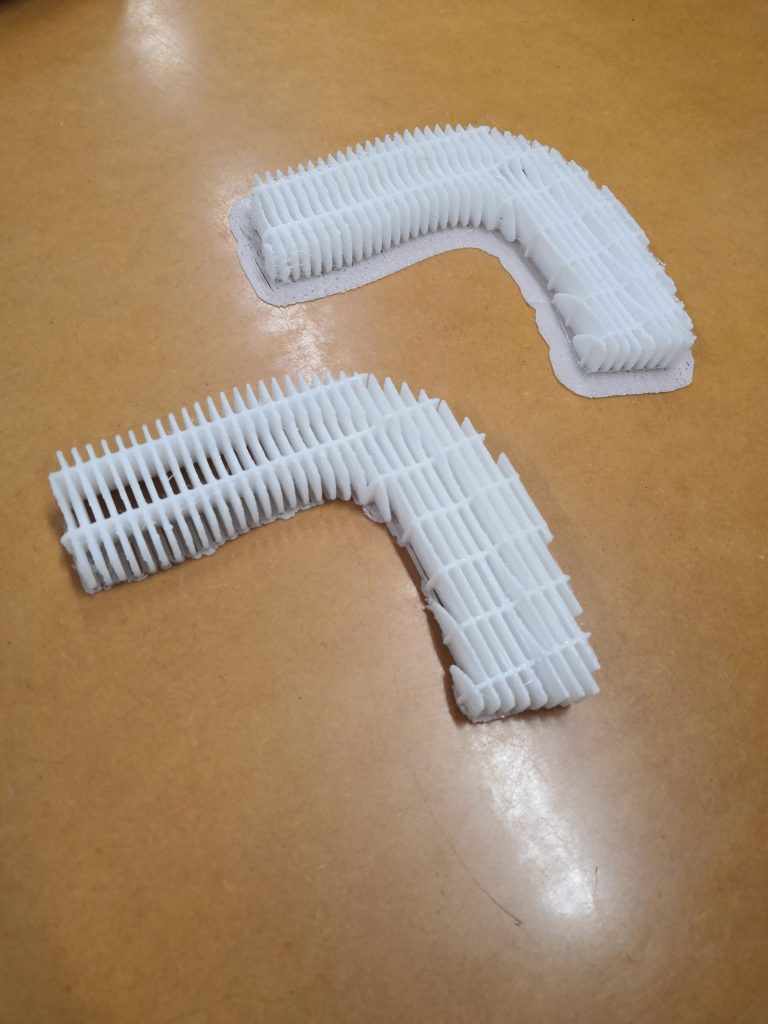
Ces documents permettent la réalisation du banc en passant par un process de 40 coupes. Mon procédé souhaitait réutiliser des matériaux de récupération, cependant ces matériaux récupérer ont des qualités différentes ce qui risquerait dans la réalisation de provoquer des ratés, « gaspillant » du temps et de la matière. De plus la réalisation d’un banc de taille moyenne nécessite tout de même de pouvoir profiter d’une grande découpeuse laser.