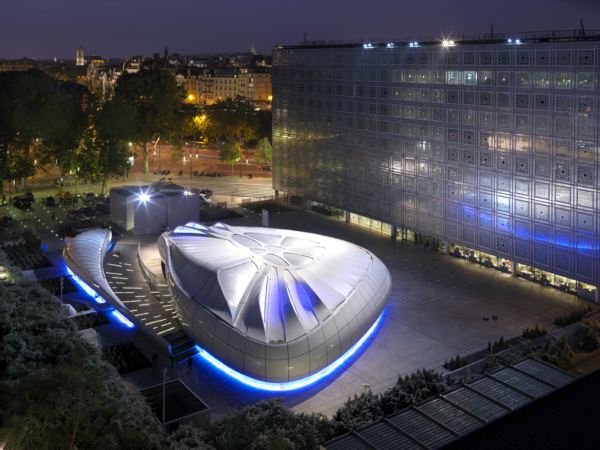
Vue extérieure du pavillon sur le parvis de l’IMA (Source)
Conçu en 2007 par Zaha Hadid Architects, le Mobile Art est un pavillon créé afin d’héberger les expositions itinérantes de la marque Chanel. Après avoir voyagé à Hong Kong, Tokyo et New York, il a été offert en 2011 à l’Institut du Monde Arabe. Sa forme organique est inspirée de motifs en spiral que l’on retrouve dans la nature. Il s’organise autour d’un volume torique ce qui permet de créer des espaces généreux. Dès l’entrée, les visiteurs découvrent une terrasse de 125 m2 puis les espaces d’exposition qui se développent dans le tore, avec en son centre, un patio de 65 m2.
CONCEPTION / MODELISATION
La complexité, les avancées technologiques dans les logiciels graphiques, ainsi que les techniques de construction, ont rendu possible l’architecture du pavillon Mobile Art qui suggère la fluidité, la nature. Ce sont les approches numériques qui nous ont permis de réaliser cette forme organique et d’échapper à l’ordre répétitif de l’architecture sérielle du XX° siècle, dominée par son aspect industriel. Zaha HADID
Dès le début du projet, l’agence Zaha Hadid Architects s’est entourée du bureau d’études structure Arup et de l’expert en construction événementielle Edwin Shirley Projects. Du fait de son caractère itinérant, le pavillon a été conçu pour être démontable et stockable dans des containers transportés ensuite par bateau ou par avion.
Afin de faciliter le développement et la réalisation du projet, Arup a réalisé une maquette 3D détaillée jusqu’au dessin des gouttières. La structure principale de 6m de haut est un véritable squelette en acier. Fait de poutres en I, il épouse la forme géométrique complexe du bâtiment et soutient les panneaux de la façade.
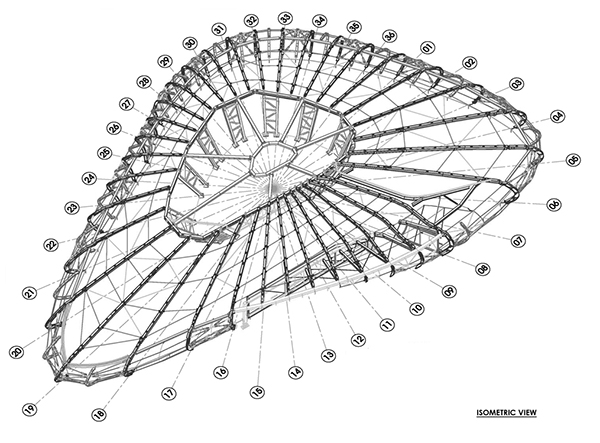
Isométrie structurelle (Source)
DISCRETISATION
Le découpage du pavillon a sûrement été dicté par l’obligation de pouvoir être transporté dans des containers de 12m. Ainsi, l’ensemble du bâtiment est démontable en 3 semaines et tient dans 56 containers.
La maquette 3D architecturale a été traduit en une maquette issue de l’analyse des éléments finis afin de permettre une réalisation efficace de la façade. Les 1300 m2 de façade ont ainsi été divisés en 425 panneaux uniques avec des géométries en 3D complexes.
MATERIAUX
Les éléments de façade ont également été dessinés sur la maquette 3D, ce qui a permis aux fabricants de produire les panneaux plus aisément et plus rapidement. Les matériaux retenus par le bureau d’étude sont le FRP (Fibre Reinforced Polymer) pour les panneaux opaques blancs, le PVC enduit de polyester pour les membranes de toit et l’ETFE (Ethylene TetraFluoroEthylene) pour les coussins transparents.
La société Stage One Limited a été chargée de fournir une alternative pour la production des panneaux courbés de la façade. Le procédé de fabrication novateur choisi pour le FRP a permis de réduire le temps de production et le coût de 50% comparé aux méthodes de fabrication de FRP traditionnelles.
D’après David Kendall d’Optima Projects chargé de la conception des panneaux FRP, ils ont été conçu pour résister à des vents extrêmes en optimisant leur structure stratifiée. Ces stratifiés ont été renforcés avec un mélange de verre comprenant des tissus biaxiaux cousus et des fibres unidirectionnelles avec différents matériaux. Des résines retardantes ont également été utilisées dans ces combinaisons. En plus de ces caractéristiques particulières, le FRP a l’avantage d’être mis en oeuvre précisément, d’être léger et robuste, ainsi que de résister à des températures supérieures à 80 °C.
Les parties transparentes du toit sont en ETFE afin de filtrer la lumière de l’espace en dessous. Ce matériaux léger et transparent permet également de couvrir des surfaces à moindre coût. Il est souple et peut être courbé pour épouser les formes uniques des coussins du toit.
When the Art Container was installed in Hong Kong, you see the skyscrapers. When installed in New York, in Central Park, you see trees. Davide Giordano, Hadid’s project architect
Le reste du toit est composé de membranes en PVC enduit de polyester qui permet de repousser l’humidité et de s’adapter aux différentes conditions climatiques et réglementaires de chaque site de l’exposition itinérante. Cette technologie utilise plusieurs couches pour former l’enveloppe externe : une membrane extérieure identique à un toit tendu normal, une membrane multi-feuilles suspendu sous le couche extérieure, et une doublure intérieure légère.
MACHINES
Toutes les installations utilisées par la société Stage One Limited sont soumises à des conditions parfaitement contrôlées et soumises au système de production ISO 9002. Ainsi, tous les moules ont été fabriqués à partir des dessins édités et contrôlés pour leur taille et leur exactitude. Chaque moule est donc unique, ce qui permet de suivre l’avancement de la production grâce à leur logiciel de suivi de construction. Les dossiers ont été gardés pour chaque lot de matériau et un échantillon de chaque application de laminé a aussi été gardé pour référence. L’attention porté au détail était essentiel mais témoigne aussi de l’efficacité de systèmes et procédures de Stage One.
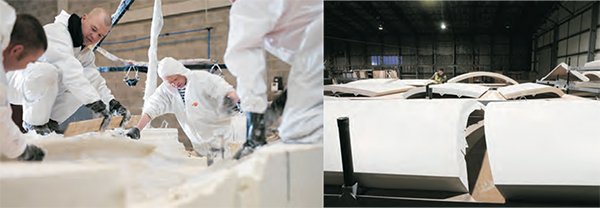
Fabrication des panneaux
Le procédé de fabrication débute avec l’usinage pour chaque panneau de moules individuels en blocs de mousse polyurethane à l’aide d’une machine CNC 5-axes. Les panneaux ont ensuite été moulés en utilisant des méthodes conventionnelles de moulage par contact. La forme géométrique obtenue était précise mais nécessitait une finition manuelle considérable avant peinture pour obtenir la finition requise.
ASSEMBLAGE
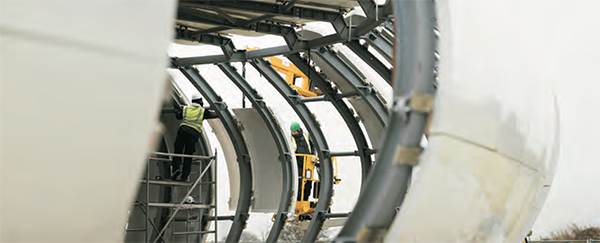
Assemblage test
Un montage test a été réalisé conjointement avec E.S. Projects. La structure métallique, 50% des panneaux FRP ainsi que les membranes de toit et le revêtement intérieur ont été installées. Après 8 semaines de montage test, le tout à été démonté, emballé et envoyé à Hong Kong pour une installation de 4 semaines.
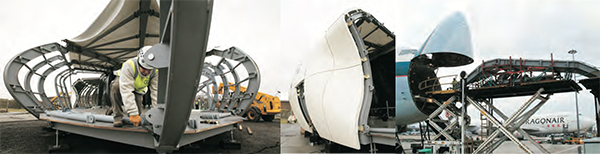
Démontage et transport
MONTAGE
A cause d’un planning très serré, l’installation requit des journées de travail de 24h. La structure a été installée en 4 semaines et, après ses 6 semaines de résidence à Hong Kong, démontée en 3 semaines avant d’être déplacée dans chaque capitale.
Vidéo du montage à l’Institut du Monde Arabe