Ce projet personnel a pour but de créer un élément d’habillage intérieur paramétré et composé de pièces reproductibles. Une fois assemblées, elles formeront une paroi « matricée ». A l’image des chemins de câblent qui habillent les couloirs de la ligne 14 du métro parisien, cet élément trouvera idéalement sa place en sous face de dalle, même si sa confection permet de l’installer aussi bien à l’horizontale qu’à la verticale. Par sa composition aléatoire et tout en volume, des jeux de textures et de lumières sont alors créés dans les circulations du bâtiment.
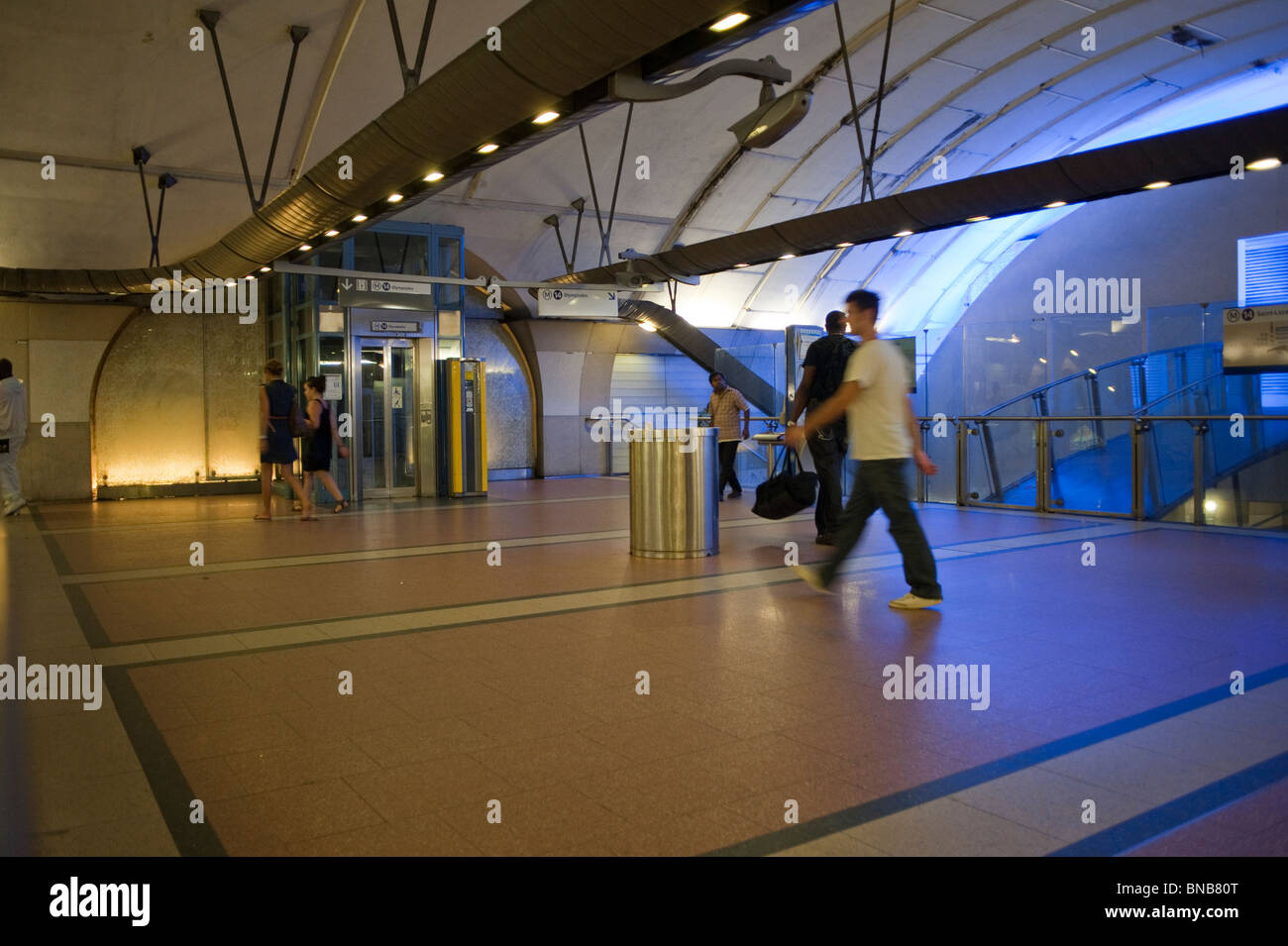
Figure 1 – Paris Métro ligne 14 : les chemins de câbles du réseau souterrain accompagnent le voyageurs dans les différents couloirs des stations.
Les inspirations paramétriques sont nombreuses et proposent toutes une approche différente. Elles ont comme point commun d’être générées à l’aide d’un logiciel dédié, comme le sujet de cet exercice.
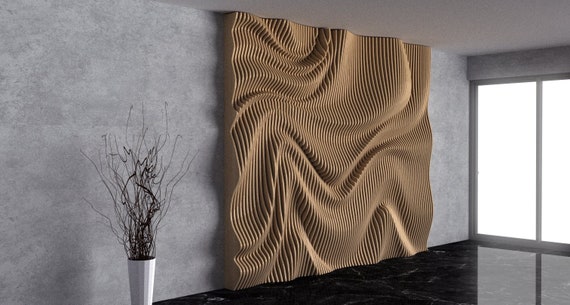
Figure 2 – Décor mural en bois ondulé, paramétrique : un exemple d’élément de décoration intérieure, paramétré et mis en contexte.

Figure 3 – élément de sous-face paramétré : si la pièce est très différente de celle réalisée dans le cadre de cet exercice, les deux ont de nombreuses similitudes : elles habillent une sous face tout en créant des jeux de volumes et lumières.
L’objet
L’objet final correspond alors à une « bande » de longueur et largeur choisies, qui vient se placer en sous-face de plancher dans le but d’habiller une circulation ou une pièce. Cette bande est décomposée en une multitude de carrés identiques qui accueillent en leur centre une extrusion. Celles-ci peut être positive (dépasse du plan, et créé un élément qui se rapproche du visiteur) comme négative (« rentre » dans le plan, et s’éloigne du visiteur). Ces variations dans la hauteur de l’extrusion sont générées aléatoirement et c’est ce qui induit les nombreux jeux de volumes.
Afin d’assurer des jeux de lumières intéressants et de rendre cette installation utile, la mise en place de LED dans les extrusions négatives permettra d’assurer un éclairage dynamique et constellé de l’espace. A l’inverse, les extrusions positives sont closes et ne laissent donc pas apparaitre de cavité.
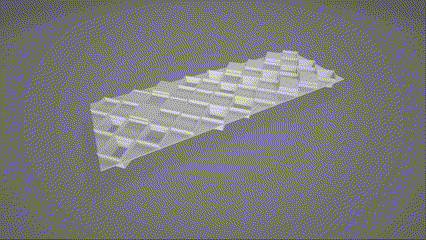
Figure 4 – Trame paramétrée : volumétrie globale d’une des itération réalisée.
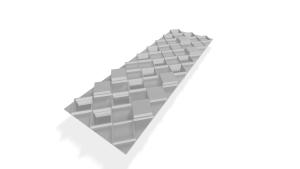
Figure 5a – Trame paramétrée : volumétrie globale d’une des itération réalisée. On distingue nettement les extrusions positives et négatives.
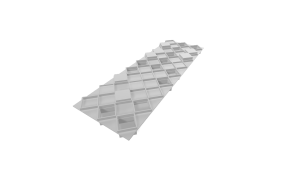
Figure 5b – Trame paramétrée : volumétrie globale d’une des itération réalisée, idem à ci-dessus mais orientée différemment.
Fonctionnement et organisation géométrique d’une pièce paramétrée.
Comme énoncé précédemment, le panneau est composé de plusieurs pièces. La première étape consiste à indiquer la longueur d’un côté d’un carré. Cela aura alors un impact significatif sur le rendu visuel général (Plusieurs dizaine de cm de côté seront adaptés à des espaces hauts de plafonds, là où quelques cm de côté offriront un rendu adapté à des passages plus confinés). Une fois que ce carré est dimensionné, il est question de savoir combien de fois il sera reporté sur la largeur ainsi que sur la longueur. Ces deux paramètres sont indépendants et permettent de former la future bande matricée.
En ce qui concerne l’extrusion, c’est un carré, pivoté de 45° par rapport à sa base et dont le côté est à égal à 0,67 fois le côté du carré principal. Le respect du théorème de Pythagore permet à ce volume d’être parfaitement inséré dans la pièce maitresse et de créer une continuité dans la trame.
Fonctionnement et organisation du programme de modélisation.
Pour réaliser cet objet, je suis passé par deux méthodes. La première consistait en la création d’une surface que l’on venait diviser par la suite. Si j’ai créé l’intégralité du code me permettant d’obtenir un résultat convaincant, je me suis heurté à plusieurs problèmes :
– L’organisation du fichier grasshopper était à revoir, car trop peu clair.
– Il était impossible d’imposer une géométrie carrée aux pièces créées, ce qui posait de nombreux problèmes de collisions dans le modèle.
– Le modèle avait du mal à s’exécuter à partir d’un trop grand nombre de répétitions.
J’ai alors fait le choix de recommencer en me basant sur le dimensionnement d’un premier carré que l’on viendrait multiplier par la suite. J’ai conservé certains éléments de code du premier script et en ai profité pour améliorer, ranger et retravailler l’ensemble.
Modélisation
On vient dans un premier temps placer un point qui servira de référentiel. Ce point est alors copié selon X puis selon Y avec une même valeur. Les deux points créés sont donc équidistants de l’origine. On additionne ces deux translations dans le but d’obtenir un quatrième point. On obtient alors un carré qu’il ne reste plus qu’à matérialiser à l’aide de l’outil surface.
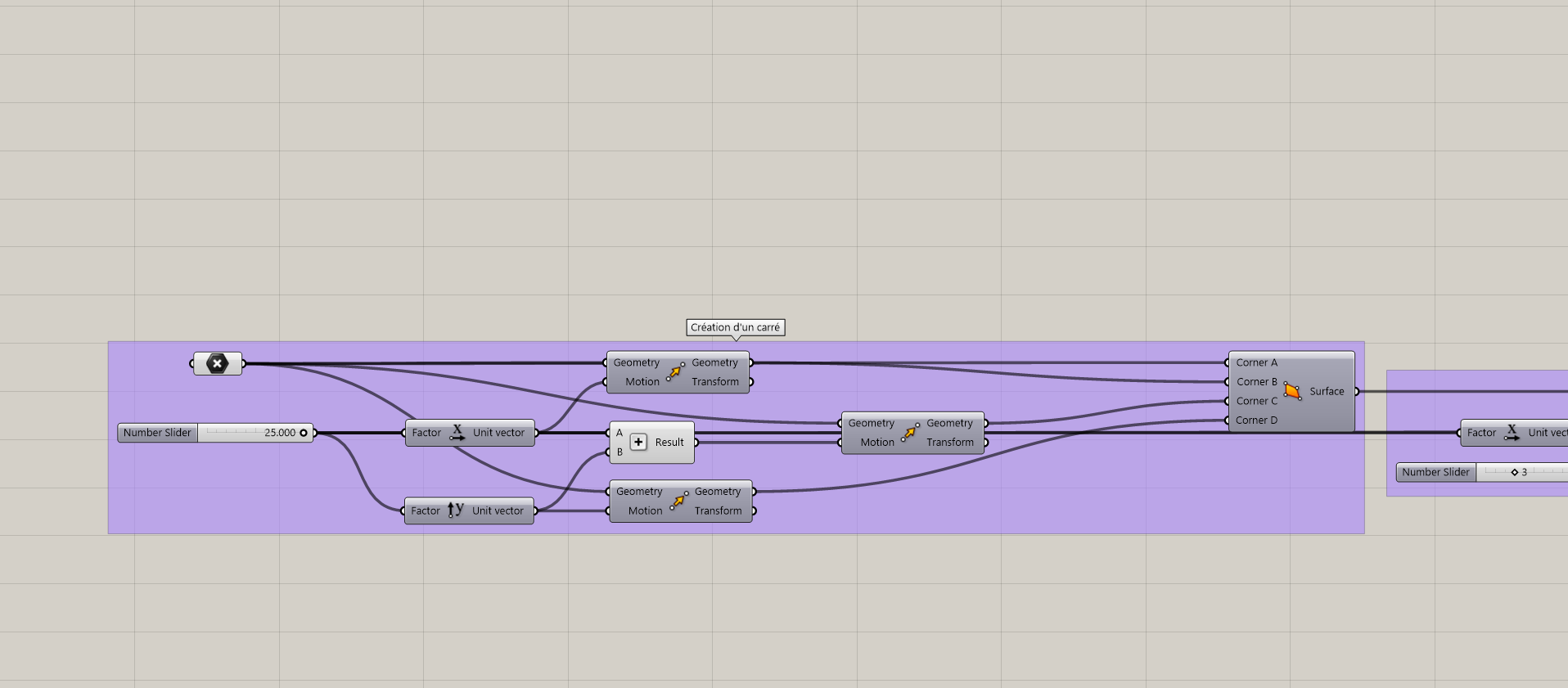
Figure 6a – Rhino + Grasshoper Script : création du carré qui servira de point de départ.
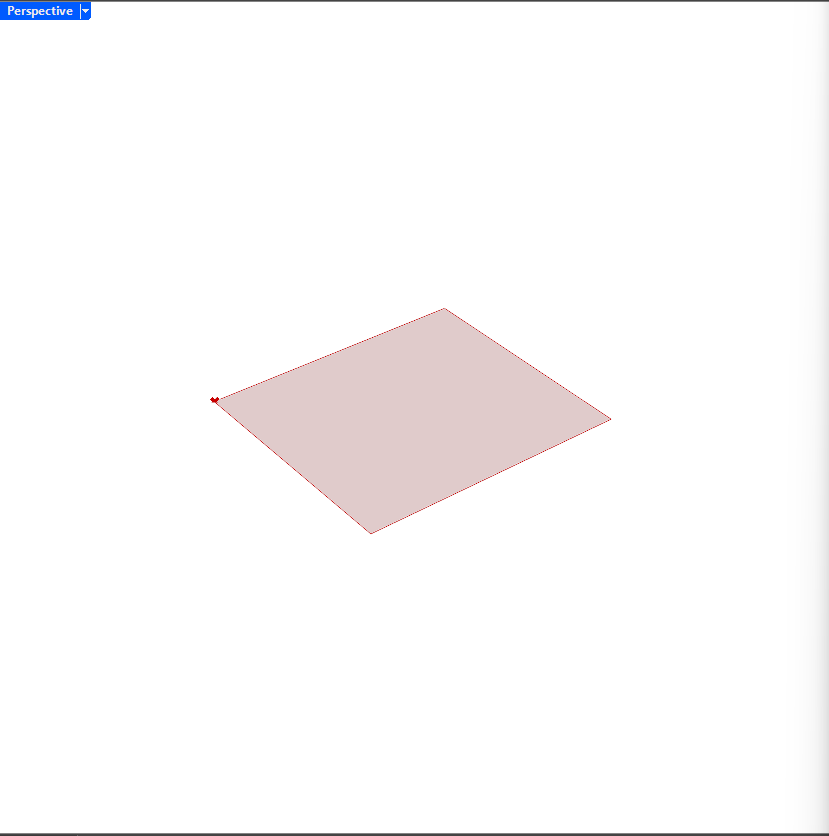
Figure 6b – Rhino + Grasshoper Script : création du carré qui servira de point de départ.
On duplique cette surface carrée un certain nombre de fois, selon X dans le but de former la largeur de la bande. On vient répéter l’action, selon Y cette fois-ci pour finir de former celle-ci. Pour s’assurer que tous les carrés sont bien jointifs, on associe les deux commandes « Linear Array » de cette étape au slider qui indique la dimension d’un carré (cf précédent). De cette façon, les points nouvellement créés sont jointifs.
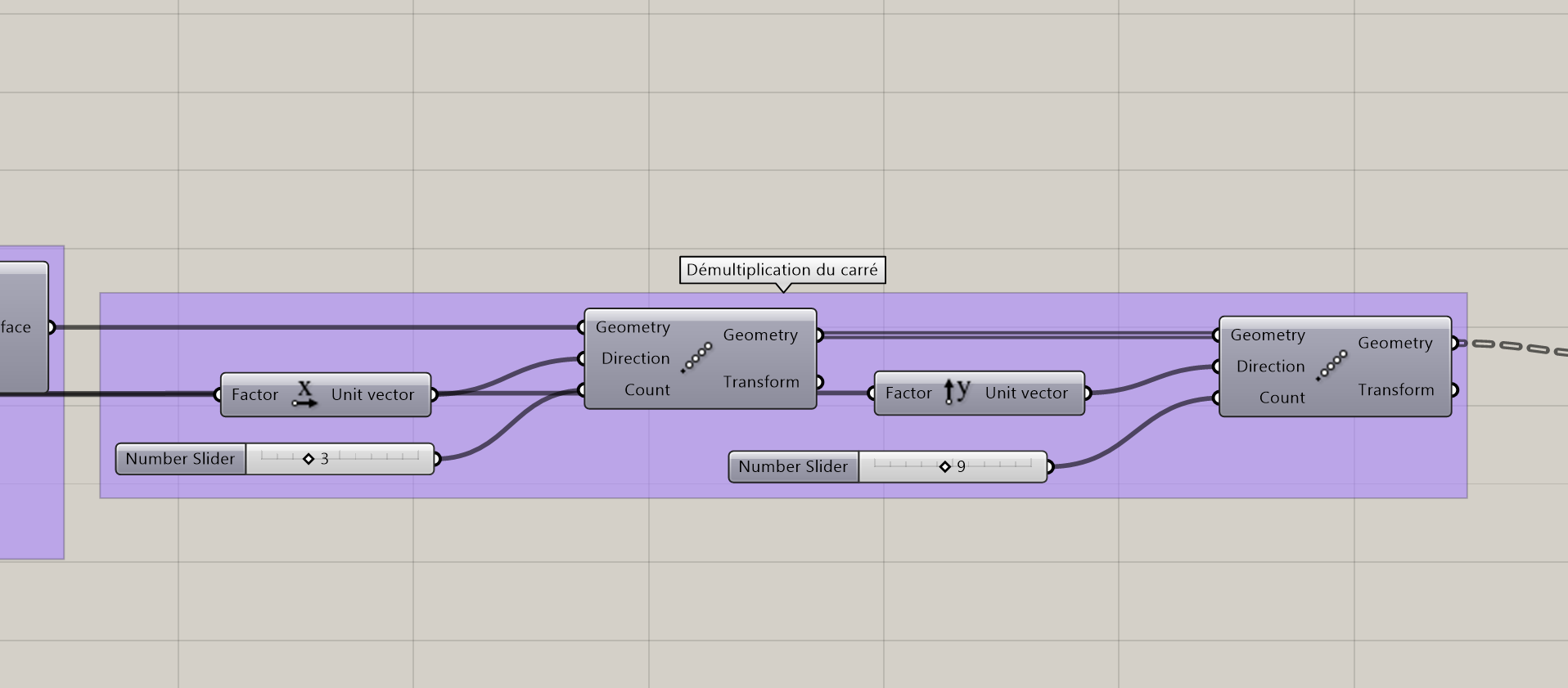
Figure 7a – Rhino + Grasshoper Script : duplication du carré de référence.
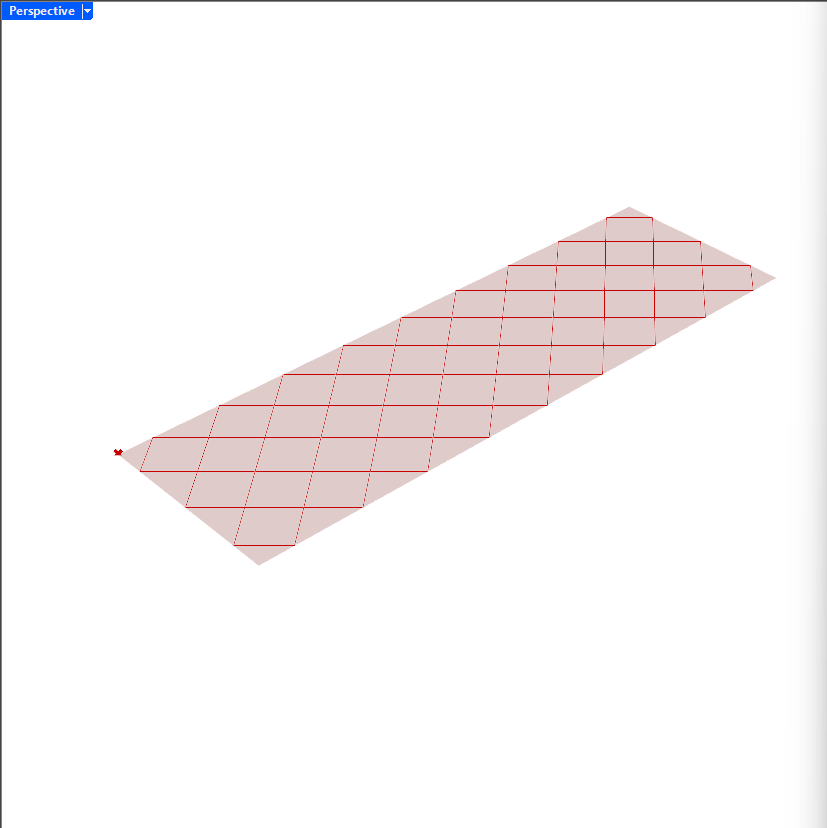
Figure 7b – Rhino + Grasshoper Script : duplication du carré de référence.
On souhaite alors réaliser des extrusions dans chacun des carrés. Le logiciel considère à cet instant qu’il n’y a qu’un seul et unique élément, ce qui ne permet pas de réaliser ces futures manipulations. On vient alors les individualiser avec la commande « Deconstruct Brep ». Il est maintenant possible de sélectionner l’ensemble à l’aide de commande « List Item » tout en s’assurant que les futurs paramètres de division seront appliqués individuellement sur chaque carré.
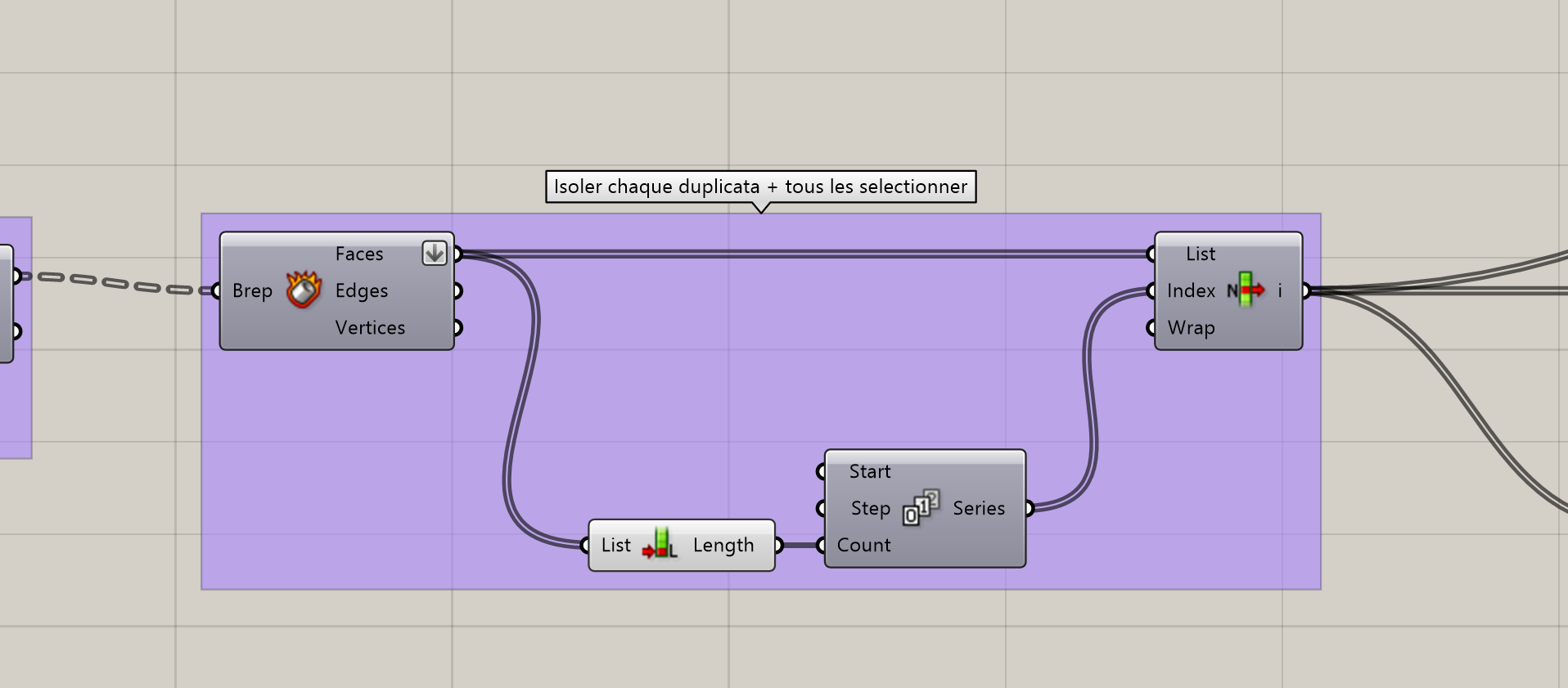
Figure 8 – Rhino + Grasshoper Script : scinder les groupes créés précédemment pour pouvoir agir dessus individuellement.
Le premier script à gauche permet de marquer l’emplacement des extrusions selon les règles mathématiques évoquées dans l’introduction (rotation de 45° de la future partie extrudée + côté de 0,67 fois la dimension du premier carré). La deuxième boite, à droite permet de venir créer une base fixe, d’une hauteur de quelques cm et qui viendra encadrer/accueillir le volume final. Nous y reviendrons par la suite, au moment d’évoquer l’assemblage. L’important est de penser à laisser de l’épaisseur dans tous les éléments extrudés pour permettre la fabrication des pièces. On utilisera alors majoritairement les commandes « Scale » pour venir marquer cette épaisseur et « solid difference » pour ne laisser que la future partie qui sera extrudée. Les scripts « extrude » selon Z peuvent alors être appliqués pour venir créer la volumétrie souhaitée.
j’ai aussi rencontré un problème au niveau de la création des volumes dans Grasshopper. La future commande « Random » présentée plus bas implique de « flatteniser » certaines données. En faisant cela, certaines opérations booléennes ne fonctionnent plus (sans que je sois capable d’en expliquer la raison, mais plusieurs témoignages en ligne laissent penser que c’est un problème récurent). Je me suis alors retrouvé avec une pièce « bouchée » par un volume qui ne pouvait être retiré via le script que j’avais préparé. Après plusieurs manipulations sans succès, j’ai trouvé une solution sur un forum. J’ai alors modifié le script pour passer par un maillage de la pièce en question. Sur ce maillage, on vient appliquer le script « Mesh difference » pour pouvoir réaliser l’opération booléenne recherchée avant de re-transformer ce maillage en surface. Le script associé à cette manipulation est présent dans les boites au dessus sur la capture d’écran.
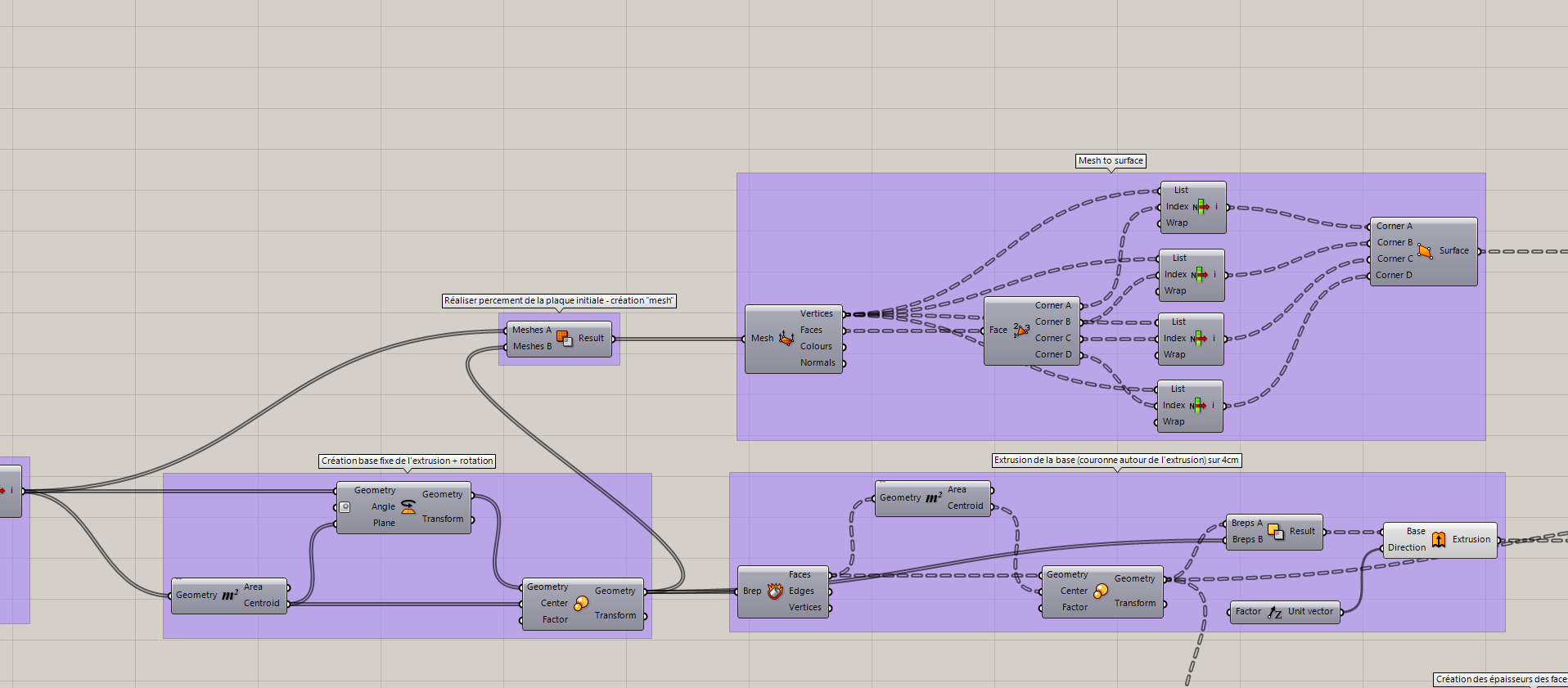
Figure 9a – Rhino + Grasshoper Script : ensemble des commandes permettant de réaliser les diverses extrusions.
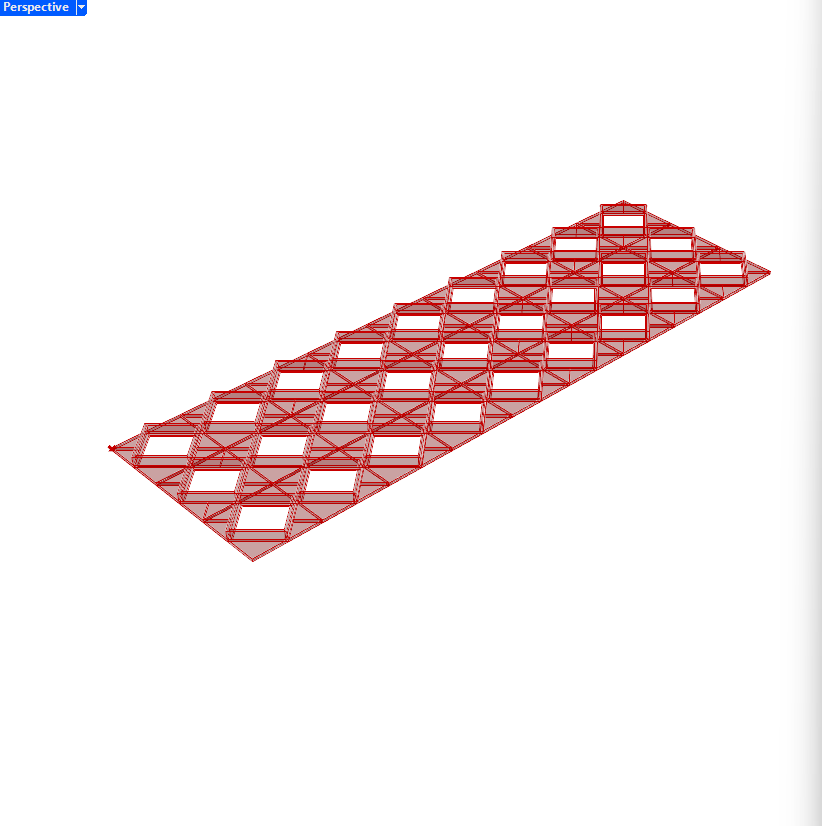
Figure 9b – Rhino + Grasshoper Script : ensemble des commandes permettant de réaliser les diverses extrusions.
A cet instant, on possède alors une première base au sein de laquelle se trouve les trous, chacun entouré d’une couronne en volume.
L’étape suivante concerne la création des volumes aléatoires. Ici aussi, il est nécessaire de venir individualiser les pièces, dans le but cette fois-ci de faire en sorte que l’aléatoire s’applique différemment sur chaque extrusion. On viendra alors réutiliser la commande « Deconstruct Brep » à l’image de ce qui a déjà été fait dans la première partie. Les deux boites les plus en bas dans la photo ci-dessous permettent de créer les côtés des extrusions. La commande « Scale » sert à la création d’une épaisseur et la commande « Solid différence » permet de venir vider le carré.
La randomisation consiste à paramétrer deux bornes limites, qui correspondent aux valeurs maximales + et – que prendront les volumes. On vient ajouter un slider (le plus en bas de la photo) qui permet de sélectionner l’itération voulue (en le faisant varier, on change l’organisation finale des volumes). Cette randomisation est associée aux volumes créés juste avant via la commande « list Item » ainsi qu’à une extrusion selon Z.
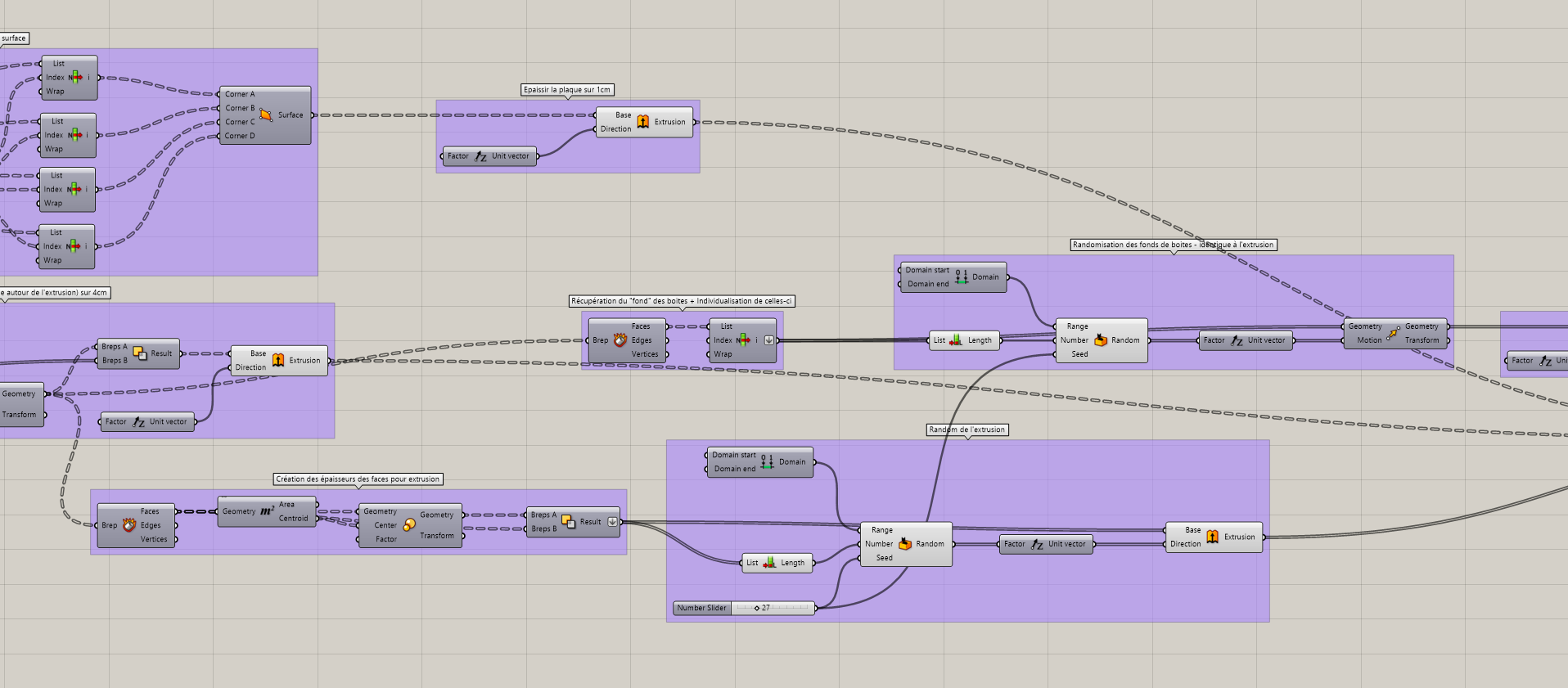
Figure 10a – Rhino + Grasshoper Script : randomiser les extrusions.
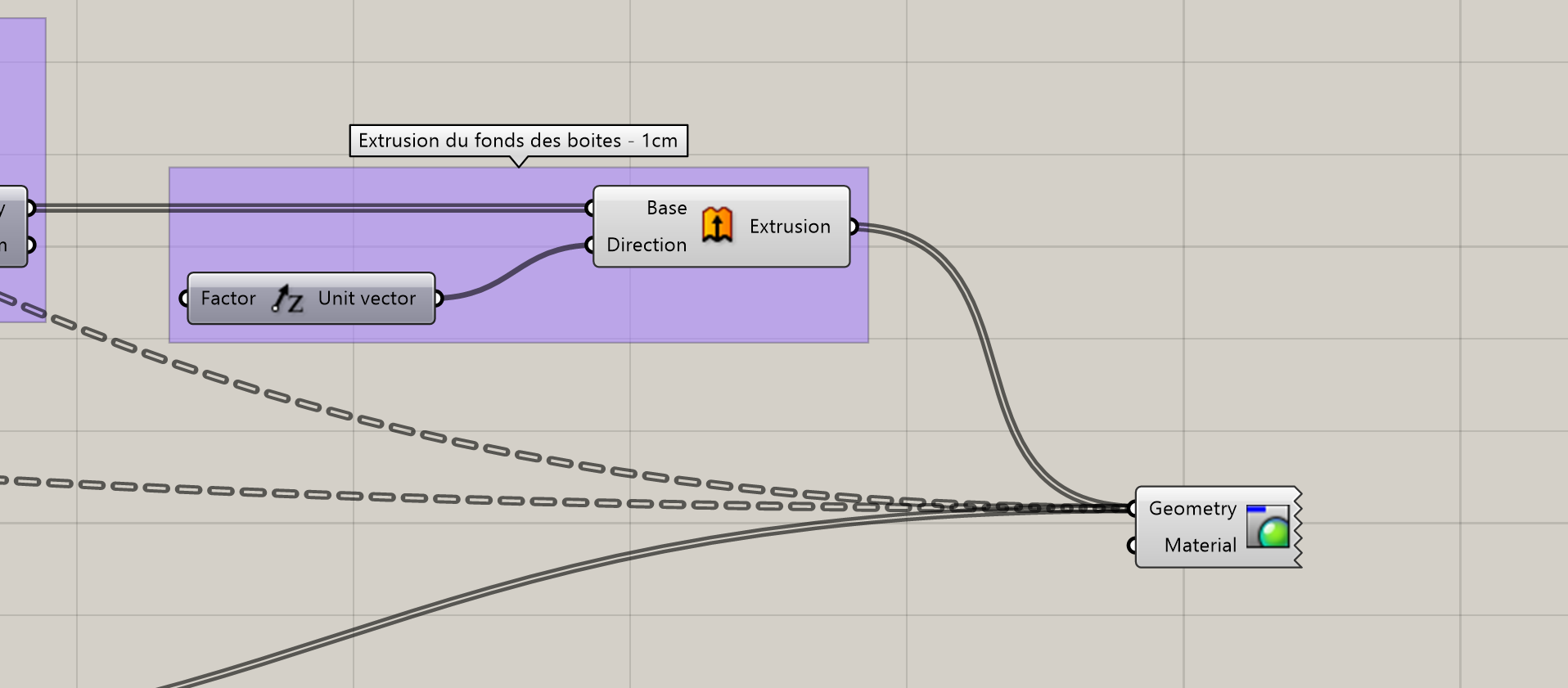
Figure 10b – Rhino + Grasshoper Script : donner du volume aux chapeaux.
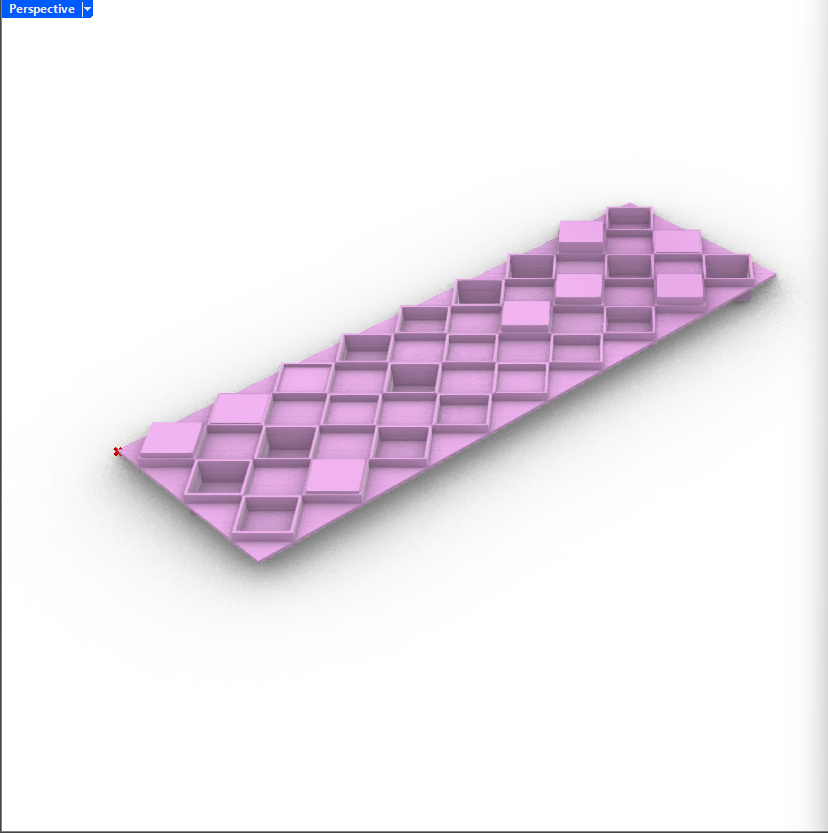
Figure 10c – Modélisation : volume final
Penser à la création de l’élément.
Après discussion autour de ce projet, il est apparu que celui-ci se trouvait entre deux interprétations possibles. La première implique un ensemble unique, « taillé dans la masse », tandis que la seconde correspond à une succession d’éléments acolés les uns aux autres. Conscient que cela peut brouiller la lecture du résultat final, j’ai choisi de travailler sur une proposition d’assemblage qui cohérente, qui s’intègre aux données fournies par le script grasshopper.
L’idée est alors de scinder la plaque qui vient accueillir les extrusions, des extrusions elles-mêmes. On profite alors du programme Grasshopper pour venir obtenir ces deux éléments et les séparer.
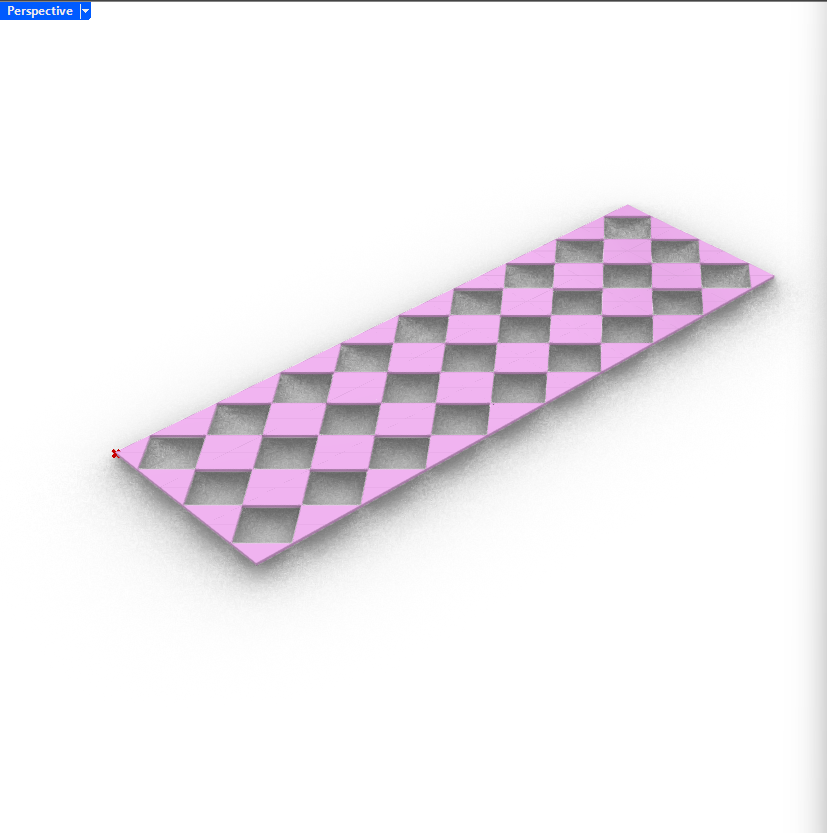
Figure 11a – Modélisation : principe d’assemblage
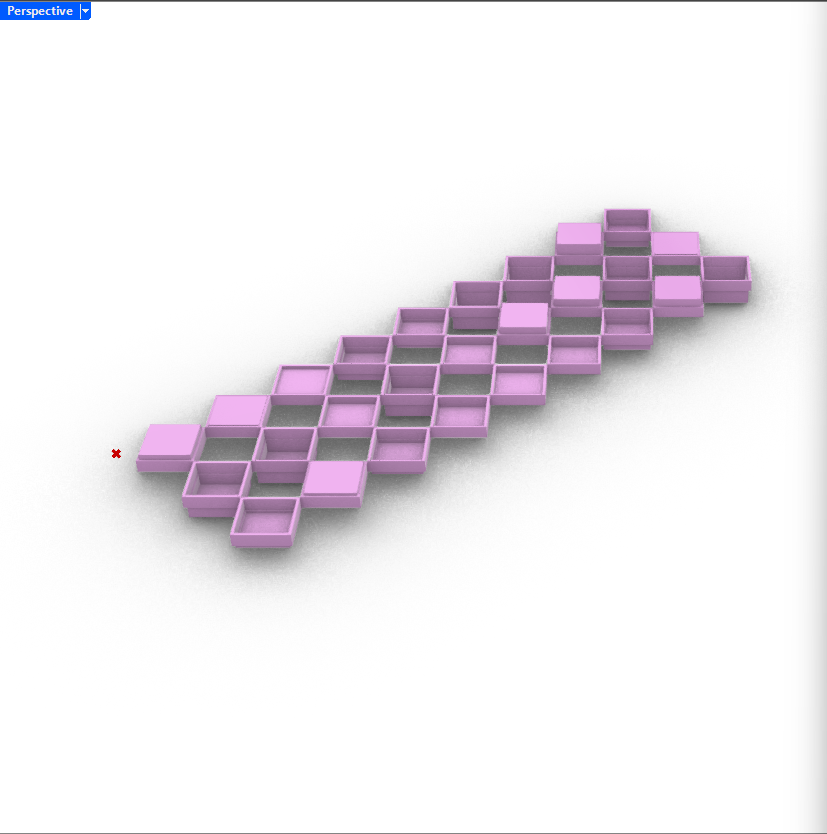
Figure 11b – Modélisation : principe d’assemblage
Les trous dans la plaque on la même dimension que les extrusions. Par conséquent, la « couronne » qui encadre ces dernières est plus large. Cet élément servira alors de point de fixation, à l’image du schéma (vue en coupe) ci-dessous. On peut envisager de coller les deux parties ou bien de mettre en place un système de vis sur la partie tournée vers le plafond (invisible pour le visiteur) si la dimension des éléments le permet.
Impression 3D et concrétisation du projet.
Il peut être intéressant de travailler avec du bois pour la réalisation de ce module, ce matériau offrant de nombreux avantages qui peuvent être exploités aisément. Dans le cadre de ce travail, j’ai fait le choix d’imprimer l’ensemble via imprimante 3D dans le but de présenter une version à une échelle réduite de la pièce.
Des photos de la maquette seront rajoutées sous peu + Des mises en situation de cet élément.
Je vous remercie pour votre lecture.
Corentin GENEST